Ask us for the best
Collaborate safely
anywhere in the world
RPC Global provides a variety of quality control and monitoring services around the world with more than 150 partner companies in this field
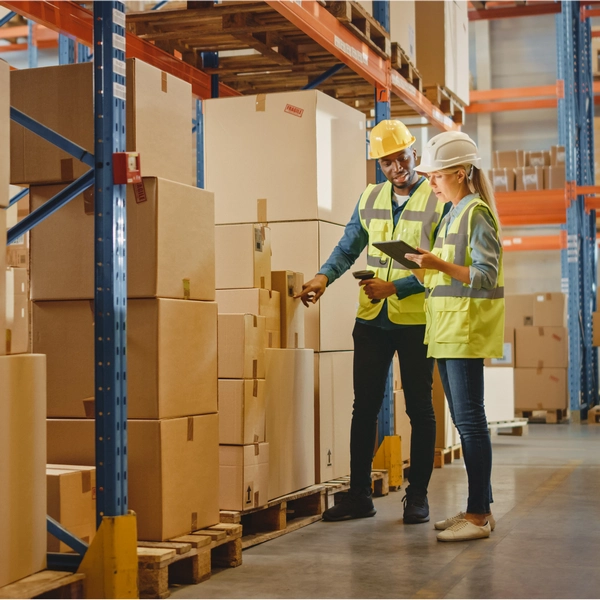
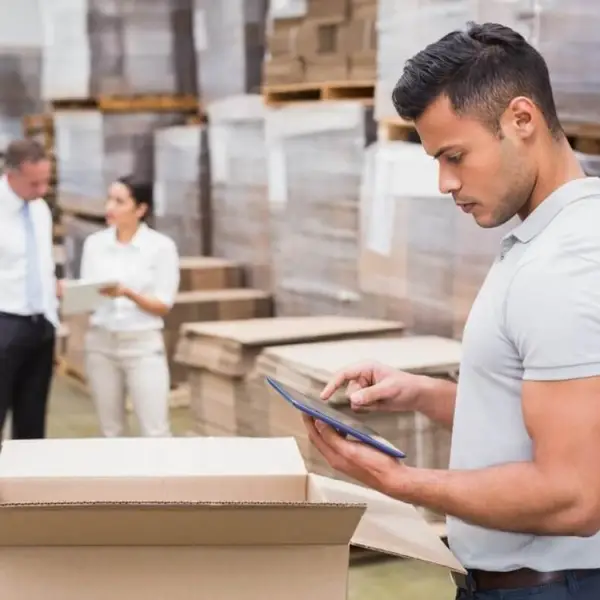
Full inspection of the number of products
During production inspection (DPI)
During Production Inspection (DPI) is a crucial quality control process conducted during the manufacturing phase to ensure that products meet specified standards and requirements. DPI involves systematic inspection and testing of materials, components, and assemblies at various stages of production. This process helps identify and rectify defects early, preventing costly rework and ensuring consistent product quality. By catching issues in real-time, DPI enhances manufacturing efficiency, reduces waste, and boosts customer satisfaction by delivering products that meet or exceed expectations. It also provides valuable insights for continuous improvement in production processes, contributing to overall operational excellence.
Inspection and testing of the production line
Final Random Inspection (FRI)
Final Random Inspection (FRI) is a quality control procedure conducted at the end of the production process, typically before the products are shipped to customers. In this method, a random sample of finished goods is selected and inspected to ensure they meet the specified quality standards and requirements. FRI helps verify that the overall production quality is consistent and acceptable, catching any remaining defects that might have been missed during earlier inspections. This process is crucial for identifying any last-minute issues, ensuring customer satisfaction, and reducing the risk of returns or complaints. By implementing Final Random Inspection, manufacturers can confidently confirm that their products are ready for market, maintaining their reputation for delivering high-quality goods.
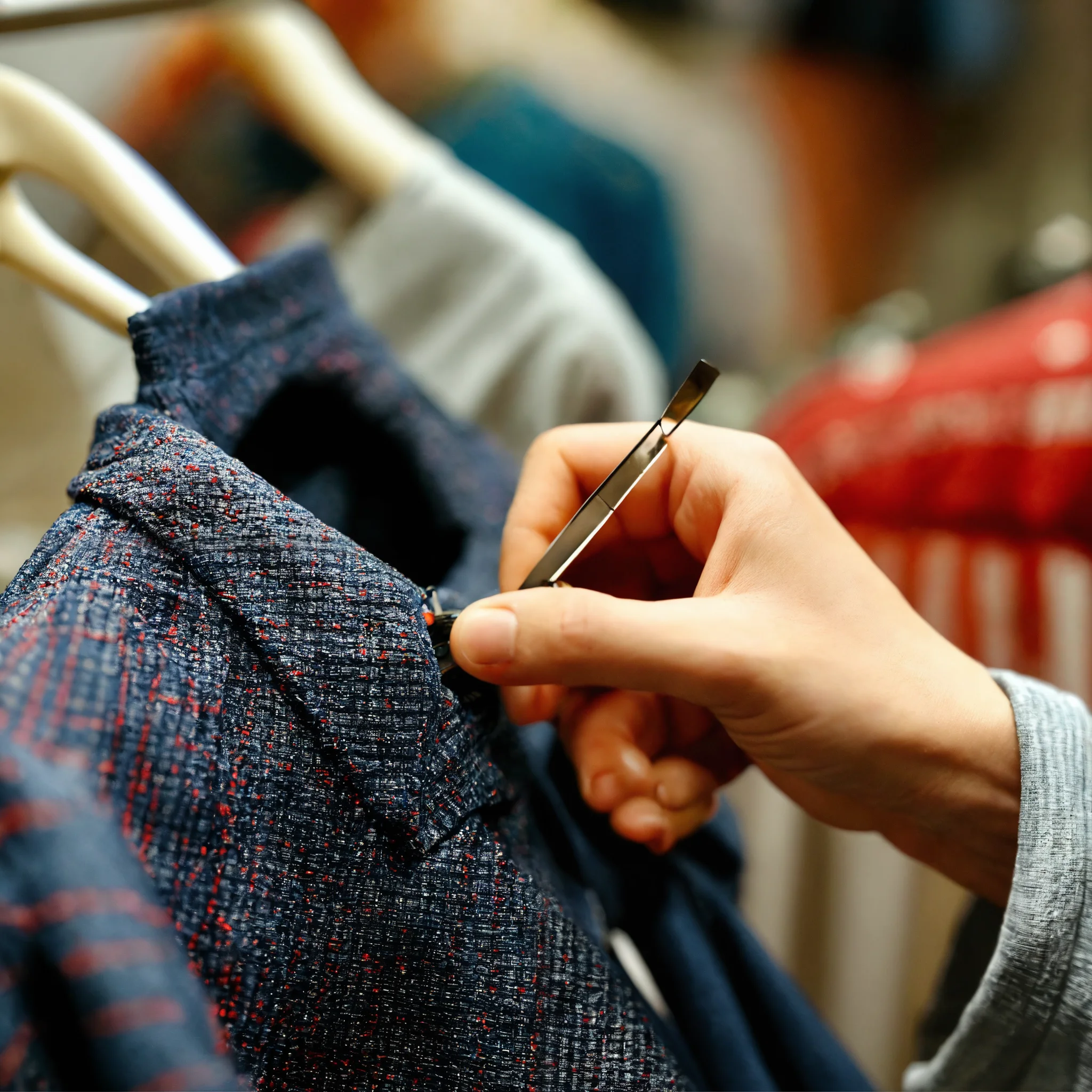
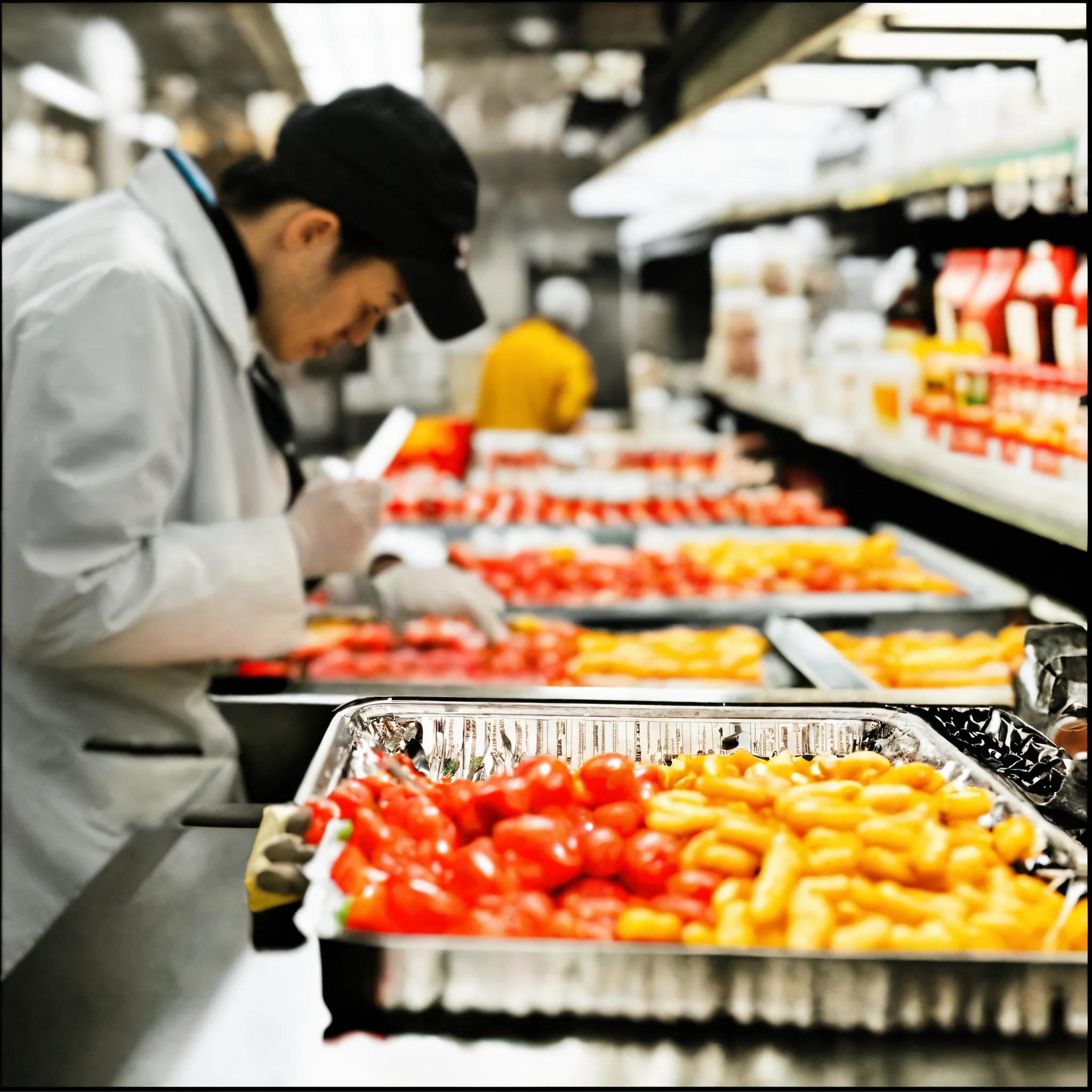
Inspection of petrochemical products
In-Process Inspection
In-Process Inspection (IPI) is a vital quality assurance practice carried out during various stages of the manufacturing process. Unlike final inspections, which occur after production is complete, IPI involves checking products, components, and processes in real-time as they are being manufactured. This proactive approach allows for the early detection and correction of defects, ensuring that any issues are addressed promptly before they escalate. IPI helps maintain consistent product quality, reduces the likelihood of costly rework, and minimizes waste. By integrating continuous monitoring and feedback into the production workflow, In-Process Inspection contributes to higher efficiency, improved compliance with standards, and greater customer satisfaction.
Inspection and testing of the production line
Full Inspection
Full Inspection is a comprehensive quality control process where every single unit of a product batch is examined to ensure it meets the specified standards and requirements. Unlike sampling inspections, which only check a portion of the batch, full inspection scrutinizes each item for defects or deviations. This meticulous approach is typically employed for high-value products, critical components, or when the cost of failure is exceptionally high. By conducting a full inspection, manufacturers can guarantee the highest level of quality and reliability, minimize the risk of defective products reaching customers, and uphold the integrity of their brand. Although more time-consuming and resource-intensive, full inspection provides unparalleled assurance of product excellence and compliance with rigorous industry standards.
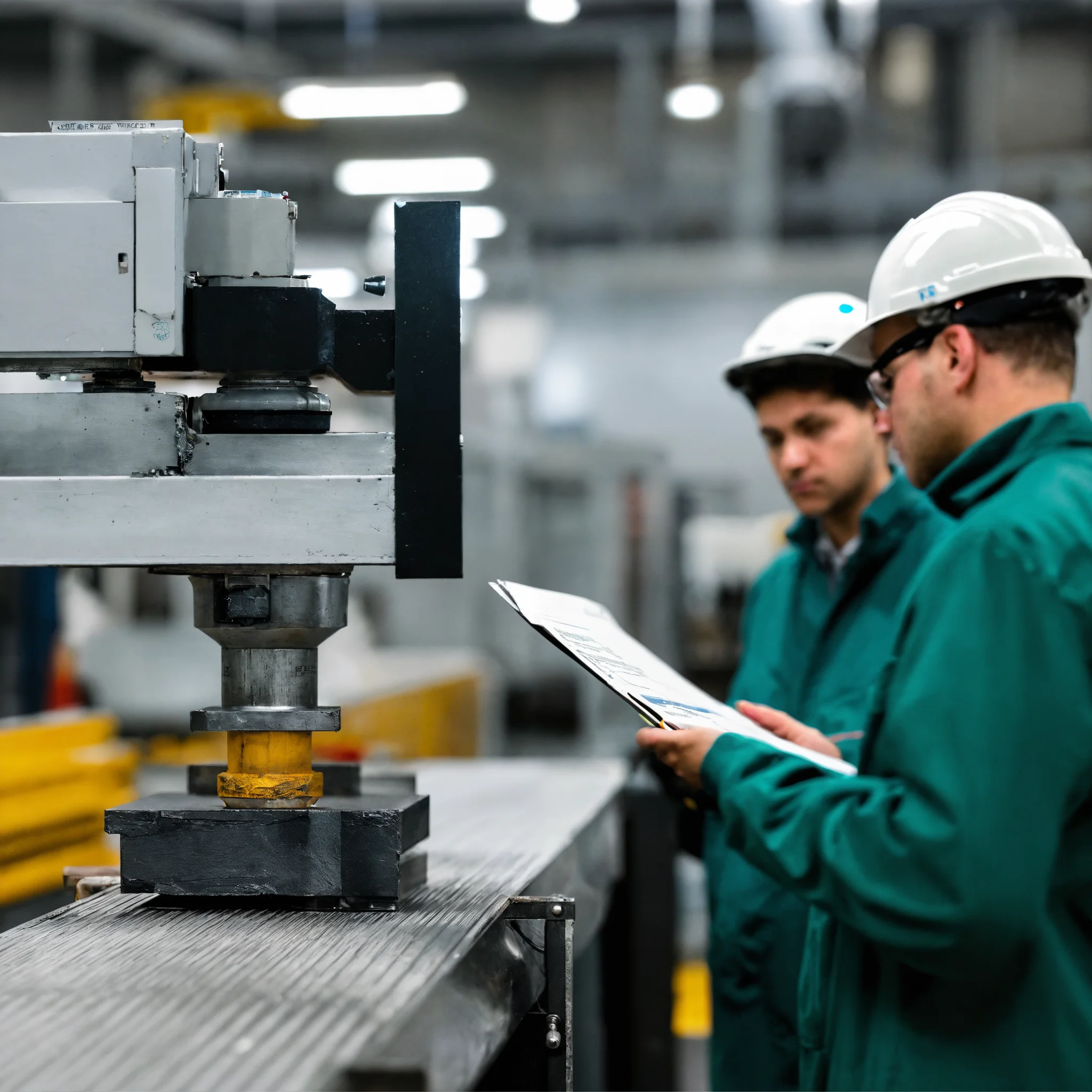
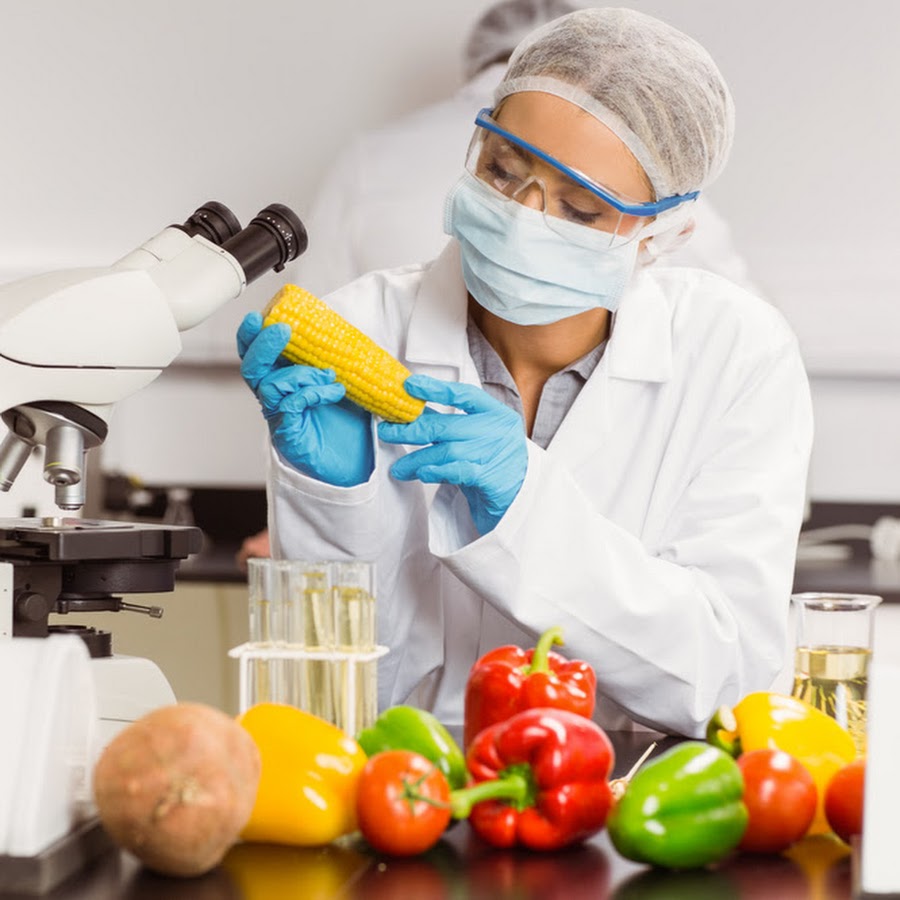
Inspection of petrochemical products
Laboratory testing inquiries
Laboratory testing inquiries involve requesting detailed information and services from laboratories to analyze and test various samples for quality, safety, and compliance. These inquiries typically cover a wide range of materials, including pharmaceuticals, chemicals, food products, and environmental samples. Through laboratory testing, clients seek to verify the properties and performance of their products, ensuring they meet regulatory standards and industry specifications. Effective communication during these inquiries is crucial to define the testing scope, methodologies, and requirements accurately. By leveraging laboratory testing inquiries, businesses can gain valuable insights into their products, enhance quality control, and ensure consumer safety and satisfaction.
Inspection and testing of the production line
Pre Shipment Inspection (PSI)
Pre-Shipment Inspection (PSI) is a critical quality control process conducted before products are shipped to the customer. This inspection occurs once the production is complete and a minimum of 80% of the order is packed for shipment. PSI involves checking the products against the purchase order specifications, including quality, quantity, packaging, labeling, and safety standards. By performing this inspection, manufacturers and buyers can identify and rectify any discrepancies or defects, ensuring that only conforming products are dispatched. This process helps prevent costly returns, enhances customer satisfaction, and maintains the supplier’s credibility. Pre-Shipment Inspection is an essential step to ensure that products meet the agreed-upon requirements and are ready for delivery to the end customer.
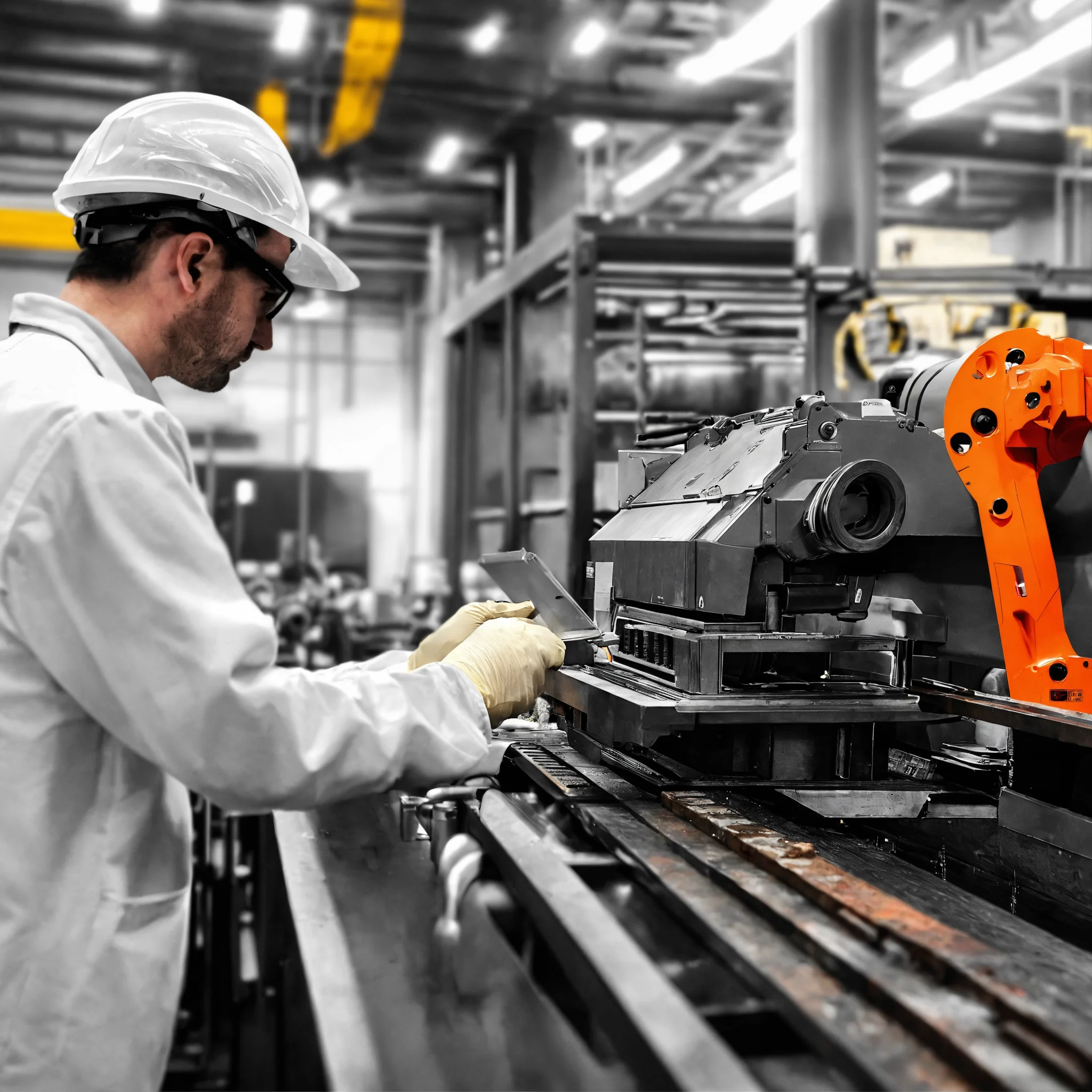
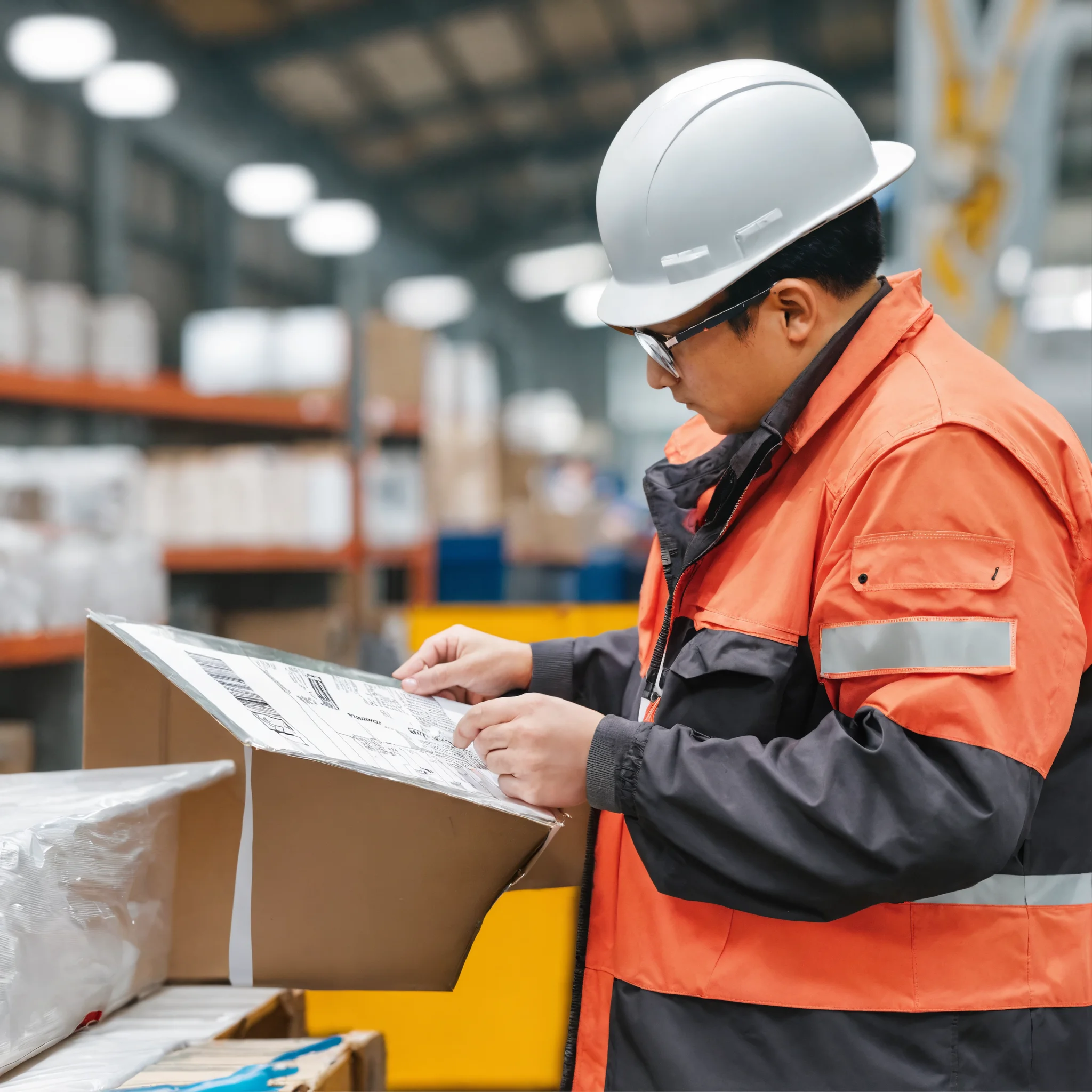
Inspection of petrochemical products
Container Loading Inspection (CLS)
Container Loading Inspection (CLI) is a crucial quality assurance process conducted during the loading of goods into shipping containers. This inspection ensures that the products are handled correctly and loaded securely to prevent damage during transit. CLI involves verifying the quantity and quality of the goods, checking for proper packaging, and ensuring that the container is clean, dry, and suitable for shipment. By performing CLI, manufacturers and exporters can confirm that the products are in good condition and that the loading process complies with the specifications and safety standards. This inspection helps minimize the risk of damage, loss, or discrepancies during shipping, thereby enhancing customer satisfaction and maintaining the integrity of the supply chain.
Inspection and testing of the production line
Ship survey (draft & alleged)
A ship survey, encompassing both draft and alleged surveys, is a comprehensive inspection process designed to assess a vessel’s condition and compliance with maritime standards. The draft survey involves measuring the ship’s draft to determine its weight and ensure it is correctly loaded, maintaining stability and safety. Alleged surveys, on the other hand, investigate specific claims or incidents, such as damage or cargo discrepancies. These surveys are essential for verifying the vessel’s seaworthiness, ensuring proper cargo handling, and resolving disputes. By conducting thorough ship surveys, maritime authorities and shipowners can uphold safety, prevent accidents, and maintain efficient and reliable shipping operations.
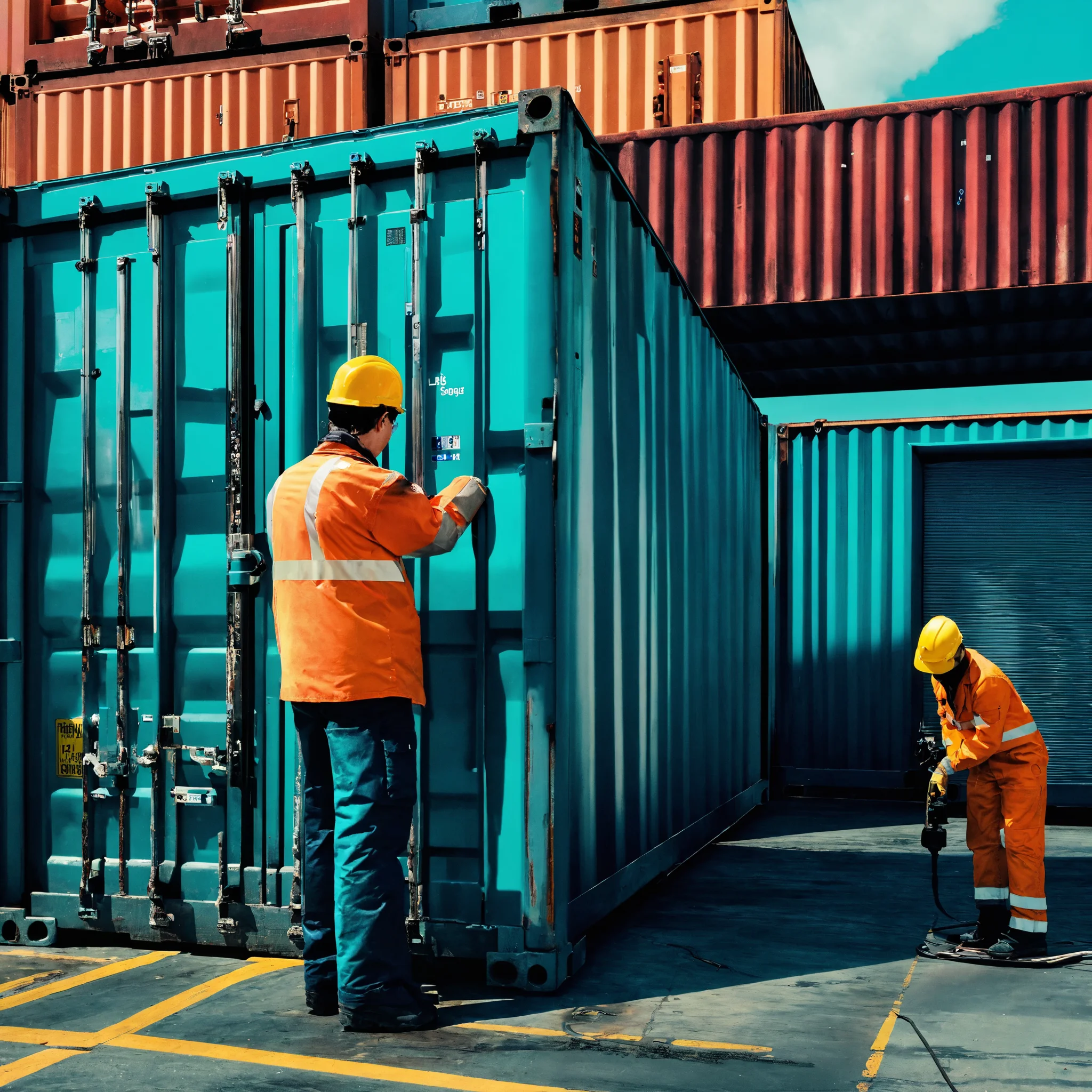
Meet Our Clients
They Believe In Us
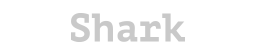
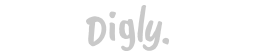
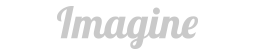
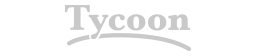
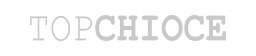
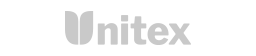
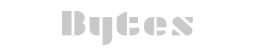
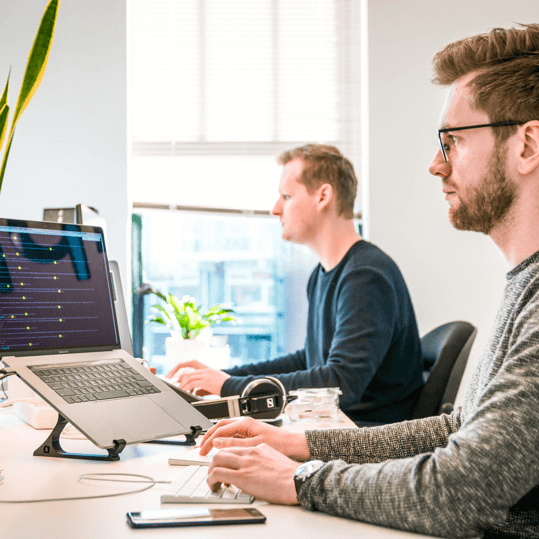